Correctly chosen connection method and refrigerant maximize the profitability of a heat pump investment
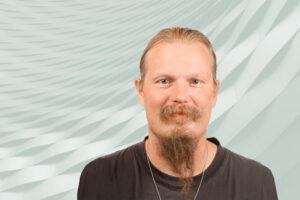
Mika Siekkinen, Fimpec’s Energy Recycling Solutions Manager, works in the midst of the accelerating heat pump boom and has seen projects grow and diversify rapidly. In this article, he highlights the importance of choosing the right refrigerant and connection method when aiming to get the most out of a heat pump investment.
The utilization of heat pumps in energy recycling is currently increasing rapidly, and new applications are constantly emerging. At Fimpec, we have been involved in designing and implementing highly interesting projects utilizing heat pump technology, including energy companies’ heat production, industrial cooling solutions, district heating solutions, utilization of waste heat from data centers, recycling waste energy from biogas plants, and the latest area of green hydrogen production facilities’ energy recycling, where heat pumps are an essential part of the process with high capacities.
The range of projects and applications is indeed extensive, and there is nothing surprising about it. Heat pump technology enables energy recycling in various sizes and types of projects. The versatility of these applications is crucial to consider when aiming for the best efficiency and the shortest possible payback period in the chosen solutions.
Two less commonly discussed but crucial choices in a heat pump project are the connection method and refrigerant. Both are related to the temperature levels of the specific case – the temperature difference between the heat source or collection side and the produced heat, as well as the variability in temperature conditions. The importance of these choices has only increased as the size of facilities grows, and the diversity of applications expands.
Temperature requirements are a crucial factor in choosing the connection method
In terms of connections, there are various options available in heat pump projects, such as parallel connection, series connection, cascade connection either with refrigerants or through an intermediate fluid, and two-stage compression connection. The most important influencing factor in the selection is the previously mentioned temperature difference between collection and production temperatures.
Parallel connection is suitable for solutions where high temperatures are not required, with a typical example being the production of 60-degree heat for a district heating network.
Series connection is a good connection method when aiming for higher temperature levels. It is a reasonable approach, for example, in utilizing waste heat from data centers, where the 20–30-degree collection heat is transformed into approximately 90-degree heat for a district heating network.
Cascade connections are well-suited for industrial applications with low collection temperatures due to process cooling, and temperature levels vary. Cascade connections offer the possibility of utilizing intermediate circuits in these cases.
Refrigerants are transitioning to natural alternatives
Regarding the refrigerants used in heat pumps, a new transition phase is underway, guided by the EU F-Gas Regulation. The regulation aims to reduce emissions of fluorinated greenhouse gases used in heat pumps and encourage the use of refrigerants with lower Global Warming Potential (GWP).
Synthetic refrigerants, especially HFO refrigerants, have been under scrutiny, and some are already prohibited. The current F-Gas Regulation does not restrict the use of HFO refrigerants, but future regulations will likely impose limitations on them as well. PFAS compound emissions will also bring restrictions to refrigerants in the future.
Natural refrigerants, such as ammonia, carbon dioxide, and pure hydrocarbons like butane and propane, are alternatives to synthetic refrigerants. There are no restrictions or prohibitions on their use in the current F-Gas Regulation. However, the drawback is the flammability of pure hydrocarbons and the toxicity of ammonia. Partly for these reasons, the use of hydrocarbons has been limited, but it has increased recently, at least in externally located devices. New alternatives are also being developed, especially for industrial solutions, and in some cases, water could be used as a refrigerant.
My standpoint is, that in a heat pump project, it is advisable not to be stuck in advance with a single refrigerant option but to consider the size and power class of the heat pump and make a decision based on that. Similarly, it is wise to prepare for the future and choose a facility that uses natural refrigerants. In our own projects, we recommend and strive to choose an option that has minimal environmental impact, with a low or zero GWP value.
Ammonia is often a good option as a refrigerant, especially in larger sizes and specific temperature ranges. Its efficiency is excellent, and good configurations can be achieved with small charges. From an environmental perspective, ammonia has no long-term greenhouse gas impact, and a GWP value of zero. In industrial solutions, it is currently the preferred option due to its good efficiency and the long lifecycle achieved with proper maintenance.
However, it must be remembered that ammonia is a toxic gas. Therefore, safety must be ensured by considering laws and regulations, standard specifications, and safety equipment such as leak detectors, emergency ventilation, and possibly necessary sprinkler systems. The risk of toxicity is reduced by the fact that ammonia dissolves well in water, so even in the event of a leak, its entry into the environment can be prevented.
Growing need for skills and competences in emerging energy systems, cooperation with educational institutions is important
Choosing the right refrigerant and connection method are good examples of the expertise needed, especially in larger-scale heat pump projects. There will be an increasing demand for this expertise and skilled professionals in the future – including at Fimpec.
Therefore, we want to contribute to the development of this expertise and engage in strong collaboration with various universities. We offer guest lectures on developing energy systems, where heat pump technology plays a crucial role. Our experts also guide thesis projects related to the field. Feel free to get in touch.
For more information:
Mika Siekkinen, Manager, Energy Recycling Solutions
Fimpec, Energy Expert Services
tel. 040 416 6610, mika.siekkinen(at)fimpec.com